Calibração de Válvulas: Como Garantir a Eficiência do Seu Sistema
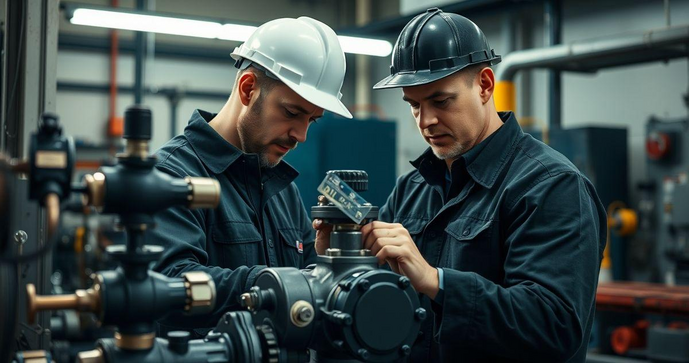
Por: Lucas - 18 de Abril de 2025
Entenda o que é calibração de válvulas e sua importância
A calibração de válvulas refere-se ao processo de ajustar as válvulas de um sistema para garantir que elas operem de acordo com as especificações desejadas. Esta técnica é crucial em diversas indústrias, incluindo petroquímica, farmacêutica e de geração de energia, pois as válvulas desempenham um papel vital no controle do fluxo de líquidos e gases.
Quando as válvulas não estão calibradas corretamente, podem ocorrer problemas sérios, como vazamentos, pressão inadequada e falhas no sistema. Isso pode comprometer a segurança dos funcionários, aumentar custos operacionais devido ao desperdício e até causar danos aos equipamentos.
Além de melhorar a segurança e a eficiência, a calibração regular das válvulas também contribui para a longevidade dos equipamentos. Ao assegurar que as válvulas funcionem de forma adequada, é possível evitar desgastes desnecessários e reduzir a necessidade de manutenção corretiva.
Em resumo, entender o que é calibração de válvulas e sua importância é fundamental para qualquer profissional que trabalhe com sistemas industriais. O processo não só aumenta a eficiência operacional, mas também protege o investimento em equipamentos e a segurança dos colaboradores.
Passo a passo para realizar a calibração de válvulas
Realizar a calibração de válvulas é um processo que deve ser feito com cuidado e precisão. A seguir, apresentamos um passo a passo para garantir que a calibração seja realizada de forma eficaz.
1. Reúna as ferramentas necessárias: Antes de começar, certifique-se de ter os equipamentos adequados, como manômetros, chave de fenda, alicate, e um dispositivo de teste para verificar a pressão e o fluxo.
2. Desconecte o sistema: Para evitar acidentes durante a calibração, é essencial desligar o sistema e liberar a pressão das válvulas. Isso garante um ambiente seguro para trabalhar.
3. Inspecione as válvulas: Antes de realizar qualquer ajuste, examine cada válvula para identificar sinais de desgastes ou danos. Qualquer válvula que apresente problemas visíveis deve ser substituída ou reparada.
4. Ajuste as configurações: Usando suas ferramentas, ajuste as válvulas conforme as especificações recomendadas pelo fabricante. Isso pode incluir modificar a pressão de abertura e fechamento, além de calibrar os pontos de ajuste.
5. Teste o sistema: Após realizar os ajustes, reconecte o sistema e ligue-o novamente. Realize testes para garantir que as válvulas estão operando de acordo com as especificações e fazem o controle correto do fluxo.
6. Documente os resultados: É importante registrar os ajustes realizados e as medições obtidas durante o processo de calibração. Esta documentação é fundamental para futuras referências e manutenções.
7. Planeje a calibração recorrente: Para garantir a eficiência contínua do sistema, estabeleça um cronograma regular de calibração, com base nas recomendações do fabricante e nas condições de operação.
Seguindo essas etapas, a calibração das válvulas pode ser realizada de forma segura e eficiente, contribuindo para o bom funcionamento do sistema.
Ferramentas necessárias para uma calibração eficiente
Para garantir uma calibração eficiente de válvulas, é essencial utilizar as ferramentas adequadas. O uso correto dessas ferramentas não só facilita o processo, mas também assegura que os ajustes sejam feitos com precisão.
1. Manômetro: Instrumento fundamental para medir a pressão do sistema. Um manômetro bem calibrado é necessário para verificar se a válvula está operando nas pressões desejadas.
2. Chave de fenda e alicate: Esses utensílios são essenciais para soltar ou apertar os parafusos das válvulas durante o processo de calibração. As chaves de fenda devem ser de diferentes tamanhos para se adequar a vários tipos de válvulas.
3. Dispositivo de Teste de Fluxo: Um testador de fluxo permite medir a quantidade de fluido que passa pela válvula, ajudando a determinar se a calibração está correta. Esse dispositivo é crucial para garantir que a válvula esteja controlando o fluxo conforme especificado.
4. Termômetro: Em sistemas que envolvem temperaturas variáveis, um termômetro pode ser necessário para medir a temperatura dos fluidos. As condições térmicas podem influenciar a operação da válvula.
5. Fluídos de Calibração: Dependendo do tipo de válvula, pode ser necessário utilizar fluidos de calibração específicos que simulem as condições reais do sistema. Essas substâncias ajudam a verificar o desempenho da válvula sob carga.
6. Equipamento de Segurança: Não se esqueça de utilizar equipamentos de segurança, como luvas e óculos de proteção. Esses utensílios são essenciais para garantir a segurança do operador durante todo o processo.
7. Software de Monitoramento: Para calibrações mais sofisticadas, o uso de software específico pode facilitar o monitoramento e a análise dos dados de calibração, permitindo ajustes mais precisos e uma gestão eficiente do sistema.
Com essas ferramentas em mãos, o processo de calibração de válvulas pode ser executado de maneira eficiente e segura, assegurando o desempenho ideal do sistema.
Fatores que influenciam a calibração de válvulas
A calibração de válvulas não é um processo isolado; vários fatores podem influenciar sua eficácia. Compreender esses fatores é fundamental para garantir que as válvulas operem conforme as especificações desejadas.
1. Temperatura: As variações de temperatura podem afetar o desempenho das válvulas, especialmente em sistemas que operam com fluidos aquecidos ou refrigerados. Condições extremas podem alterar a viscosidade dos fluidos, impactando a precisão do controle de fluxo.
2. Pressão do Sistema: A pressão interna do sistema é crucial para o funcionamento das válvulas. Pressões muito altas ou muito baixas podem interferir na calibração, resultando em um controle ineficiente. É vital monitorar e ajustar a calibração de acordo com as pressões operacionais.
3. Tipo de Fluido: O tipo de fluido que passa pela válvula (líquido, gás, corrosivo) pode ter um grande impacto na calibração. Fluidos viscosos ou particulados podem causar obstruções e desgastes, exigindo um ajuste mais frequente da calibração.
4. Desgaste e Manutenção: O estado físico da válvula e seu desgaste natural ao longo do tempo influenciam diretamente a precisão da calibração. Válvulas que não recebem manutenção regular podem desenvolver problemas que afetem sua operação, como vazamentos ou falhas mecânicas.
5. Condições Ambientais: Fatores externos, como umidade, poeira e temperatura ambiente, podem afetar a calibração das válvulas. Ambientes agressivos podem acelerar o desgaste e a corrosão, exigindo calibrações mais frequentes.
6. Variação na Configuração do Sistema: Mudanças na configuração do sistema, seja por alterações na tubulação ou componentes adicionais, podem impactar diretamente a calibração. Toda modificação deve ser considerada durante o processo de calibração para garantir que as válvulas operem adequadamente.
7. Interferência de Equipamentos Adjuntos: Equipamentos como bombas e compressores que interagem com as válvulas podem afetar seu desempenho. A calibração deve considerar a interação entre esses dispositivos, assegurando que todo o sistema trabalhe em harmonia.
A consciência desses fatores pode aumentar significativamente a eficiência operacional e a segurança das válvulas, tornando a calibração um processo mais eficaz e minimizando os riscos de falhas no sistema.
Sinais de que suas válvulas precisam de calibração
Identificar os sinais de que as válvulas precisam de calibração é essencial para garantir a eficiência e segurança do sistema. Conhecer esses sinais pode ajudar na tomada de decisões proativas sobre manutenção.
1. Vazamentos Visíveis: Um dos sinais mais claros de que uma válvula precisa de calibração é a presença de vazamentos. Isso pode indicar que a válvula não está fechando corretamente ou que há problemas internamente.
2. Flutuação na Pressão: Se a medição da pressão apresenta flutuações inesperadas, isso pode indicar uma calibração inadequada. A pressão deve se manter dentro de limites específicos, e oscilações podem ser um sinal de falha no controle da válvula.
3. Ruídos Anormais: Barulhos estrondosos ou incomuns ao operar a válvula podem ser um indicativo de que a calibração não está em conformidade. Esses ruídos podem resultar de componentes internos desgastados ou mal ajustados.
4. Atrasos no Abertura e Fechamento: Quando o tempo que a válvula leva para abrir ou fechar se torna inconsistente, isso pode ser um sinal de que ajustes são necessários. A resposta da válvula deve ser rápida e adequada às exigências do sistema.
5. Dificuldade em Manter o Fluxo: Se há dificuldades em manter um fluxo constante, isso indica que a válvula pode estar mal calibrada. O monitoramento do fluxo é essencial e qualquer anomalia deve ser investigada.
6. Mudanças no Diâmetro do Fluxo: Alterações visíveis no diâmetro do fluxo, como redução ou aumento inesperado, podem sinalizar que algo está errado com a calibragem da válvula. Essas mudanças devem ser acompanhadas para evitar falhas no sistema.
7. Alarmes de Segurança: Se alarmes de segurança são ativados frequentemente sem uma causa aparente, isso pode sugerir problemas na calibração das válvulas. A investigação imediata deve ser feita para evitar riscos maiores.
Reconhecer esses sinais com antecedência pode evitar falhas significativas no sistema e garantir que a calibragem das válvulas seja realizada quando necessário, contribuindo assim para operações eficientes e seguras.
Benefícios da calibração regular de válvulas
A calibração regular de válvulas oferece uma série de benefícios que vão além da simple manutenção do equipamento. Esses benefícios são cruciais para garantir o funcionamento eficiente e seguro dos sistemas.
1. Aumento da Eficiência Operacional: A calibração frequente garante que as válvulas funcionem dentro dos parâmetros ideais, resultando em um controle de fluxo eficiente. Isso permite que os sistemas operacionais funcionem de forma otimizada, reduzindo o consumo de energia e melhorando a produtividade.
2. Redução de Custos com Manutenção: Manter as válvulas calibradas pode minimizar a necessidade de reparos grandes e dispendiosos. A detecção precoce de problemas durante a calibração pode evitar falhas maiores que exigem despesas significativas.
3. Aumento da Vida Útil dos Equipamentos: A calibração regular ajuda a identificar desgastes e problemas antes que se tornem críticos. Isso reduz o estresse nos componentes, aumentando sua vida útil e diminuindo a frequência de substituições.
4. Garantia de Segurança: Válvulas mal calibradas podem levar a vazamentos e falhas perigosas, colocando em risco a segurança dos operadores e do ambiente. A calibração regular assegura que as válvulas funcionem corretamente, contribuindo para um ambiente de trabalho seguro.
5. Melhoria na Qualidade do Produto: Em indústrias onde a precisão é fundamental, a calibração de válvulas tem um impacto direto na qualidade do produto final. A calibração adequada garante que os processos de produção atendam a padrões rigorosos, resultando em produtos de alta qualidade.
6. Conformidade com Regulamentações: Muitas indústrias têm normas rigorosas que devem ser seguidas. A calibração regular ajuda as empresas a estarem em conformidade com esses regulamentos, evitando multas e complicações legais.
7. Menor impacto ambiental: Um sistema bem calibrado opera de maneira mais limpa e eficiente, reduzindo o desperdício de recursos e minimizando o impacto ambiental. Isso se alinha com práticas sustentáveis e responsabilidade corporativa.
Em resumo, os benefícios da calibração regular de válvulas são abrangentes e impactam diretamente a eficiência operacional, a segurança e a sustentabilidade do sistema. Investir na calibração é fundamental para garantir que os processos industriais funcionem sem interrupções.
A calibração de válvulas é uma prática essencial que não deve ser negligenciada em qualquer sistema operacional. Compreender sua importância e os fatores que influenciam esse processo é fundamental para garantir que os sistemas funcionem de maneira eficiente e segura.
Realizar calibrações regulares traz diversos benefícios, desde a melhoria da eficiência operacional até a segurança dos operadores e a qualidade do produto final. Identificar sinais de que as válvulas precisam de calibração pode prevenir problemas maiores e reduzir custos a longo prazo.
Investir em calibração não é apenas uma questão de manutenção; é uma estratégia inteligente que potencializa a eficiência e a durabilidade dos equipamentos, contribuindo para um desempenho otimizado do sistema. Adotar práticas de calibração contínua é um passo importante para qualquer organização que busca excelência em suas operações.