Calibração de Válvulas: Como Garantir Precisão e Desempenho
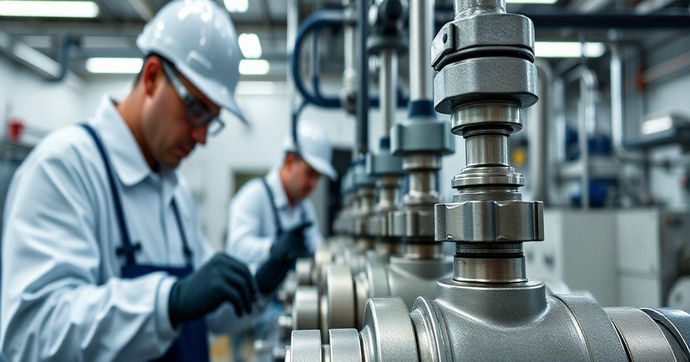
Por: Lucas - 29 de Dezembro de 2024
Calibração de válvulas é um procedimento crucial para garantir o funcionamento eficiente e seguro de diversos sistemas industriais e comerciais. Neste artigo, você aprenderá sobre a importância da calibração, os tipos de válvulas disponíveis, além de dicas práticas e um guia passo a passo para realizar esse processo de forma correta. Continue lendo para descobrir como manter suas válvulas em perfeito estado e evitar problemas que podem comprometer a operação de suas máquinas.
Importância da Calibração de Válvulas
A calibração de válvulas é um aspecto fundamental que não pode ser ignorado em qualquer sistema industrial que utiliza este tipo de componente. Ela desempenha um papel significativo na eficiência, segurança e confiabilidade de operações que dependem de válvulas para regular o fluxo de líquidos e gases. Neste artigo, iremos explorar a importância da calibração de válvulas e os impactos que ela pode ter em um ambiente de trabalho.
Uma válvula descalibrada pode levar a resultados indesejados e até mesmo perigosos. Por exemplo, um equipamento pode não funcionar corretamente, levando a possíveis falhas na produção, perda de matérias-primas e até riscos à segurança dos funcionários. Além disso, a calibração inadequada pode resultar em desperdícios significativos e em uma operação global menos eficiente.
Quando as válvulas estão calibradas corretamente, elas são capazes de controlar o fluxo de maneira precisa. Isso é especialmente importante em indústrias onde a pressão e a temperatura precisam ser mantidas dentro de parâmetros rigorosos. A calibração assegura que esses parâmetros sejam alcançados e mantidos, evitando assim os problemas que poderiam ocorrer com uma operação mal calibrada.
Um exemplo prático da importância da calibração de válvulas pode ser visto em sistemas que utilizam Pressostato industrial, onde a precisão no controle de pressão é crítica. Se as válvulas não estiverem calibradas corretamente, o pressostato pode não operar dentro das especificações desejadas. Isso pode provocar uma série de incidentes, como falhas na automação do sistema ou até mesmo explosões em sistemas de alta pressão. Nesse cenário, a calibração de válvulas atua como uma salvaguarda, garantindo que todos os componentes do sistema funcionem em harmonia.
Além dos riscos operacionais, a calibração de válvulas também pode ter implicações financeiras significativas. As indústrias estão constantemente buscando maneiras de reduzir custos e aumentar a eficiência. Equipamentos que operam mal podem consumir mais energia e requerer manutenção mais frequente, resultando em despesas adicionais. Ao garantir que as válvulas sejam calibradas regularmente, as empresas podem otimizar o consumo de energia e prolongar a vida útil dos equipamentos, economizando dinheiro a longo prazo.
Outro aspecto importante da calibração de válvulas é a conformidade com as normas e regulamentações de segurança. Muitas indústrias estão sujeitas a rigorosos padrões de segurança que exigem a calibração regular de equipamentos. Caso uma auditoria revele a falta de calibração, a empresa pode enfrentar não apenas multas pesadas, mas também um grande danos à sua reputação. Assim, manter os processos de calibração em dia é essencial para a credibilidade e sustentação de um negócio no mercado.
A calibração das válvulas não deve ser vista como uma tarefa isolada ou de baixo custo; ela deveria ser uma parte integral da rotina de manutenção. Para garantir resultados eficazes, a calibração deve ser realizada por profissionais qualificados e com experiência na área. A escolha de um bom fornecedor de serviços de calibração, que utilize tecnologias apropriadas e siga as melhores práticas do setor, é vital para obter resultados satisfatórios.
Em resumo, a calibração de válvulas é uma prática de suma importância que impacta diretamente a eficiência operacional, segurança no trabalho e a economia dentro de uma indústria. Desde a redução de custos até a conformidade com as regulamentações, a calibração desempenha uma função central em garantir que todos os sistemas operem com a máxima performance. Portanto, é fundamental que as empresas reconheçam a importância dessa prática e a implementem em seus procedimentos operacionais padrão. Ao adotar uma abordagem proativa em relação à calibração de válvulas, elas não apenas protegem seus ativos, mas também asseguram um ambiente de trabalho mais seguro e produtivo.
Principais Tipos de Válvulas e Seus Usos
As válvulas são componentes cruciais em vários sistemas industriais e de automação, desempenhando um papel vital no controle de fluxo e pressão de líquidos e gases. Existem muitos tipos de válvulas disponíveis, cada uma projetada para um propósito específico e permitindo uma ampla gama de aplicações. Neste artigo, exploraremos os principais tipos de válvulas, suas características e os usos mais comuns em diferentes setores.
Um dos tipos mais comuns de válvulas é a válvula de esfera. Esta válvula é famosa por sua capacidade de permitir ou interromper o fluxo de forma rápida e eficaz, utilizando uma esfera oca que se move dentro do corpo da válvula. As válvulas de esfera são frequentemente utilizadas em sistemas de encanamento, onde a rapidez de abertura e fechamento é essencial, como em indústrias de processamento de alimentos e petróleo.
Outro tipo muito popular é a válvula de globo, que é projetada para regular o fluxo de forma contínua. Comumente utilizada em aplicações onde é necessário um controle mais preciso do fluxo, a válvula de globo apresenta um design que permite a modulação do fluxo através de um movimento axial de um disco. Esses dispositivos são frequentemente encontrados em aplicações de aquecimento, ventilação e ar condicionado (HVAC), onde a precisão na temperatura do fluxo é crucial.
A válvula borboleta é outra opção bastante utilizada em sistemas que armazenam e transportam líquidos ou gases. Este tipo de válvula pode ser aberto ou fechado por meio de um disco circular que gira em um eixo, permitindo um controle eficaz do fluxo. As válvulas borboleta são frequentemente empregadas em sistemas de irrigação e em indústrias químicas, onde há necessidade de operar em condições de alta pressão.
Além das válvulas acima, vale a pena mencionar a Válvula solenoide para água, que desempenha um papel fundamental em sistemas automatizados. Essas válvulas são controladas eletronicamente e são frequentemente utilizadas em sistemas de irrigação, aquecimento e em processos automatizados de controle de líquidos. Por serem acionadas por um eletroímã, as válvulas solenoides são capazes de abrir e fechar rapidamente, tornando-as ideais para aplicações que exigem alta frequência de operação.
As válvulas de retenção são outras importantes que não podem ser esquecidas. Elas têm a função de permitir o fluxo em apenas uma direção, impedindo o retorno do fluido. Esse tipo de válvula é vital em sistemas de bombeamento, onde é necessário evitar o refluxo para garantir a eficiência do sistema. Em aplicações industriais, as válvulas de retenção são frequentemente localizadas após as bombas, ajudando a manter a pressão apropriada e a evitar danos aos equipamentos.
As válvulas reguladoras de pressão são essenciais em sistemas onde a pressão do fluido precisa ser mantida dentro de limites específicos. Essas válvulas podem ser ajustadas para liberar pressão quando necessário, o que é fundamental em sistemas de gás industrial e em aplicações químicas. Elas ajudam a proteger tanto o sistema interno quanto os operadores, evitando situações de risco devido a pressões excessivas.
Por fim, as válvulas de alívio ou segurança são projetadas para aliviar a pressão em um sistema e são fundamentais em instalações que lidam com fluidos pressurizados. Essas válvulas atuam como uma linha de defesa contra falhas catastróficas, liberando pressão excessiva para evitar explosões ou vazamentos perigosos. Elas são frequentemente utilizadas em refinarias de petróleo, usinas químicas e sistemas de gás industrial, onde a segurança é uma prioridade máxima.
Em resumo, as diferentes categorias de válvulas desempenham funções essenciais em diversos setores e sistemas. Desde o controle de fluídos até a proteção do sistema contra pressões perigosas, cada tipo de válvula é projetado para atender necessidades específicas de controle e segurança. É fundamental que as empresas escolham o tipo adequado de válvula para suas operações, a fim de garantir eficiência, segurança e longevidade no uso do equipamento. Assim, compreender a diversidade de válvulas disponíveis e seu funcionamento é crucial para qualquer profissional que atue em setores industriais e de automação.
Ferramentas Necessárias para Calibração
A calibração de válvulas é um procedimento essencial para garantir a eficiência e segurança de sistemas industriais. Para executar esse procedimento de forma correta, é fundamental contar com as ferramentas apropriadas. Neste artigo, iremos explorar as principais ferramentas necessárias para a calibração de válvulas, o papel de cada uma delas e como sua aplicação pode impactar a qualidade do processo de calibração.
Uma das ferramentas mais importantes para a calibração de válvulas é o manômetro. O manômetro é utilizado para medir a pressão do fluido que passa pela válvula. Com ele, é possível determinar se a válvula está funcionando dentro dos parâmetros de pressão especificados. Existem diferentes tipos de manômetros, incluindo analógicos e digitais, e a escolha do tipo apropriado dependerá das necessidades específicas do sistema em questão.
Outra ferramenta essencial é o calibrador de pressão. Este dispositivo é utilizado para gerar e medir a pressão durante o processo de calibração. Um calibrador de pressão preciso permitirá que o técnico ajuste a válvula de acordo com as especificações do fabricante. Muitos calibradores de pressão modernos são digitais e oferecem uma leitura mais precisa, além de facilitar a realização de várias medições em um curto espaço de tempo.
Os Tubos aço carbono também são frequentemente utilizados durante a calibração de válvulas. Eles são essenciais para conectar diferentes componentes do sistema e garantir que o fluido possa se mover de forma eficiente através da válvula. Ás vezes, essas conexões são feitas utilizando mangueiras flexíveis, mas os tubos de aço carbono oferecem uma solução resistente e durável para sistemas que lidam com pressões elevadas e altas temperaturas.
A chave de torque é outra ferramenta vital que não pode faltar na lista de equipamentos necessários para a calibração. A chave de torque é utilizada para apertar ou soltar os parafusos na montagem da válvula de acordo com um torque específico, evitando assim danos ao equipamento. É crucial garantir que os parafusos estejam devidamente ajustados, pois uma montagem incorreta pode levar a vazamentos e falhas no sistema. Usar uma chave de torque calibrada garante que o processo seja feito de acordo com os padrões exigidos.
Instrumentos de medição de temperatura também são frequentemente utilizados na calibração de válvulas, especialmente em sistemas onde a temperatura do fluido é um fator crítico. Termômetros ou sensores de temperatura podem fornecer leituras em tempo real, permitindo que o operador verifique se a válvula está operando dentro da faixa desejada. Meios de regulação de temperatura são fundamentais em aplicações industriais, como em processos químicos e de aquecimento.
Câmaras de teste são outra ferramenta que pode ser utilizada para a calibração de válvulas. Estas câmaras permitem que os técnicos simulem condições específicas de operação, como pressão e temperatura, para avaliar como a válvula se comporta nessas circunstâncias. Isso é especialmente útil quando se trabalha com válvulas que operam em condições extremas, onde o comportamento real pode variar significativamente de uma situação normal.
Além dessas ferramentas, é importante ter à disposição equipamentos de proteção individual (EPIs) adequados. A calibração de válvulas pode envolver o manuseio de fluidos pressurizados e potencialmente perigosos, portanto, o uso de EPIs como luvas, óculos de proteção e roupas adequadas é indispensável para garantir a segurança dos profissionais envolvidos no procedimento.
Outra ferramenta que contribui para um processo de calibração eficiente é o software de monitoração e controle. Em sistemas modernos, ferramentas de software podem ajudar a registrar dados de calibração e monitorar previamente os parâmetros de operação. Esses dados podem ser utilizados para análises estatísticas, facilitando a identificação de padrões e a detecção de problemas antes que se tornem críticos.
Em resumo, a calibração de válvulas é um processo complexo que requer uma variedade de ferramentas apropriadas para ser realizado corretamente. Desde manômetros e calibradores de pressão, até tubos de aço carbono e chaves de torque, cada ferramenta desempenha um papel crucial no sucesso do procedimento. Garantir que todas as ferramentas necessárias estejam disponíveis e em bom estado de funcionamento é essencial para assegurar resultados precisos e confiáveis. Ao investir nas ferramentas adequadas e seguir as melhores práticas de calibração, as empresas podem garantir a segurança, eficiência e longevidade de seus sistemas industriais.
Passo a Passo da Calibração de Válvulas
A calibração de válvulas é um processo essencial que garante a eficácia e a segurança do funcionamento de sistemas industriais. É um procedimento que, quando realizado corretamente, pode prevenir falhas operacionais e uma série de problemas relacionados ao controle de fluxo e pressão. Neste artigo, iremos descrever o passo a passo da calibração de válvulas, proporcionando um guia prático que você pode seguir em suas operações.
Antes de iniciar o processo de calibração, é importante preparar o ambiente de trabalho. Certifique-se de que todas as ferramentas necessárias estão à mão, incluindo manômetros, calibradores de pressão e, se aplicável, a Válvula esfera tripartida para realizar testes seguros. Também é essencial garantir que o local esteja livre de obstruções e que o acesso aos equipamentos seja facilitado para evitar acidentes durante o procedimento.
O primeiro passo na calibração de válvulas é desligar o sistema. Isso é crucial para garantir a segurança durante todo o processo, pois permite que você trabalhe sem a pressão do fluido interferindo nas medições. Feche a fonte de alimentação e certifica-se de que não há pressão residual no sistema, permitindo que o fluido escape com segurança. Isso pode ser feito através da abertura de válvulas de sangria, se houver.
Uma vez que o sistema esteja seguro, o próximo passo é inspecionar a válvula. Verifique visualmente se há sinais de desgaste, corrosão ou danos. Isso é importante porque uma válvula danificada pode não funcionar corretamente, mesmo após a calibração. Se qualquer problema for identificado, considere substituir a válvula ou realizar reparos antes de proceder com a calibração.
Em seguida, é hora de conectar o manômetro ao ponto de teste da válvula. O manômetro deve ser instalado de forma a assegurar uma leitura precisa da pressão. Após a conexão, ligue novamente o sistema e permita que a pressão estabilize antes de prosseguir. Isso é fundamental para garantir que as medições que você está prestes a realizar sejam acuradas.
Depois que a pressão estiver estabilizada, você deve começar a abrir a válvula lentamente. Observe as leituras do manômetro enquanto a válvula abre. Anote a pressão em que a válvula começa a permitir o fluxo e as pressões em diferentes aberturas da válvula até a abertura total. Esses dados são cruciais para a calibração, pois ajudarão a estabelecer a relação entre a posição da válvula e a pressão do fluido.
Com as medições feitas, o próximo passo é comparar os dados coletados com as especificações do fabricante. Cada válvula possui características operacionais específicas, e é essencial que você entenda esses parâmetros para fazer os ajustes necessários. Se a válvula não estiver atendendo às especificações exigidas, será necessário realizar ajustes.
Para ajustar a válvula, você pode precisar utilizar um calibrador de pressão. Dependendo do tipo de válvula e do sistema, você deverá aumentar ou diminuir a pressão na entrada da válvula até que ela atinja as configurações desejadas. Realize os ajustes lentamente, sempre monitorando as leituras do manômetro para que os resultados obtidos sejam precisos e confiáveis.
Depois de fazer os ajustes necessários, é importante repetir a medição. Feche a válvula novamente e abra-a uma vez mais para garantir que a calibração foi bem-sucedida. Se os resultados ainda não estiverem dentro das especificações, pode ser necessário repetir o processo de calibração ou investigar mais profundamente a causa do problema.
Uma vez que a calibração tenha sido concluída com sucesso, é essencial realizar um teste final de integração no sistema. Isso envolve colocar a válvula de volta em operação e monitorar seu desempenho sob condições normais. Verifique se as pressões e fluxos estão dentro dos parâmetros definidos. Este teste é crucial para garantir que não apenas a válvula esteja calibrada, mas também que ela funcione perfeitamente em conjunto com o restante do sistema.
Por último, não se esqueça de documentar todo o processo de calibração. Anote todos os dados coletados, ajustes realizados e resultados dos testes. Essa documentação é fundamental não apenas para futuras referências, mas também para cumprir exigências de conformidade e manutenção do sistema. Manter registros precisos pode ajudar a prever quaisquer problemas futuros e a garantir que a manutenção preventiva seja realizada de forma adequada.
Em conclusão, a calibração de válvulas é um procedimento crítico que requer cuidado e atenção aos detalhes. Seguir este passo a passo pode ajudar a garantir que você realize a calibração de forma eficaz, mantendo a segurança e a eficiência do sistema. Ao realizar a calibração de válvulas de maneira sistemática, você estará contribuindo para a longevidade e a confiabilidade das operações de sua fábrica ou instalação industrial.
Sinais de Que a Calibração é Necessária
A calibração de válvulas é uma parte essencial da manutenção de sistemas industriais e comerciais. É um processo que assegura que as válvulas estão operando dentro dos parâmetros especificados, garantindo eficiência e segurança. No entanto, há momentos em que a calibração se torna necessária, e é fundamental reconhecer esses sinais o mais cedo possível. Neste artigo, vamos explorar os principais indicadores de que a calibração de válvulas é necessária, permitindo que você tome ações corretivas antes que problemas maiores ocorram.
Um dos sinais mais evidentes de que a calibração de válvulas é necessária é a presença de vazamentos. Se você perceber que há fluido escapando ao redor da válvula, isso pode indicar que a vedação não está mais eficaz, resultando em uma pressão inadequada. Vazamentos não apenas prejudicam a eficiência do sistema, mas também podem ser perigosos, especialmente em ambientes industriais onde fluidos perigosos estão presentes. Se você notar vazamentos, é recomendável verificar a calibração imediatamente, além de inspecionar as configurações de vedação da válvula.
Outro sinal claro de que a calibração é necessária é a mudança no desempenho do sistema. Se a válvula não está abrindo ou fechando adequadamente, ou se há uma variação inesperada na pressão, isso pode indicar que a válvula não está calibrada corretamente. Uma válvula que não está respondendo como deveria pode levar a sobrecargas ou subcarregas em outras partes do sistema, o que, por sua vez, pode causar falhas operacionais. Sem uma calibração adequada, o risco de danos e falhas aumentará. Portanto, fique atento a qualquer mudança no desempenho geral do sistema.
A variação na medição de pressão também é um sinal de alerta. Se as leituras do medidor não estiverem alinhadas com o esperado ou se houver flutuações inesperadas, isso pode significar que a válvula não está mantendo a pressão correta. Medidores de pressão descalibrados podem fornecer leituras erradas, fazendo parecer que o sistema está funcionando corretamente, quando na realidade corre o risco de falhar. Se você perceber discrepâncias nas leituras, é hora de realizar uma verificação completa no sistema, incluindo a calibração das válvulas.
Os ciclos de operação da válvula também fornecem pistas valiosas sobre a necessidade de calibração. Se você notar que a válvula está tendo um aumento no número de ciclos de abertura e fechamento, isso pode ser um sinal de que ela não está funcionando de modo otimizado. Válvulas que se desgastam tendem a exigir um esforço maior para se movimentar, e isso pode levar a um aumento no tempo gasto em cada ciclo. Esse problema pode ser causado por uma calibração inadequada ou por falhas no componente, e é crucial não ignorá-lo para evitar dificuldades futuras.
Outro sinal importante é a inconsistemcia na temperatura do fluido. Se você notar que a temperatura do fluido que passa pela válvula não está dentro das faixas normalmente esperadas, isso pode indicar que a válvula não está regulando o fluxo corretamente. As válvulas são frequentemente utilizadas para controlar a temperatura em sistemas de aquecimento e resfriamento, e uma calibração falha pode levar a superaquecer ou a subresfriamentos, comprometendo o desempenho do sistema e podendo causar danos irreparáveis.
Além disso, os ruídos incomuns durante o funcionamento da válvula também são um sinal de que a calibração pode ser necessária. Se você ouvir ruídos estrondosos, estalos ou vibrações incomuns, pode ser um indicativo de que a válvula está estressada ou enfrentando dificuldades em operar adequadamente. Esses problemas devem ser abordados rapidamente, pois podem indicar falhas mecânicas ou a necessidade de uma melhor calibragem.
A falta de manutenção regular também é um fator que deve ser levado em consideração. Sistemas que não são mantidos regularmente correm o risco de ter suas válvulas descalibradas com o tempo. Um cronograma regular de manutenção e calibração é vital para garantir o desempenho contínuo e seguro de qualquer sistema. Se não houver um histórico de calibrações anteriores, pode ser o momento certo para implementar uma verificação completa para garantir que todos os componentes estejam funcionando dentro de suas especificações.
Por último, fique atento a padrões de performance. Se você identificar que a eficiência do sistema está em declínio gradualmente, mas sem soluções evidentes, isso pode ser um sinal de que a calibração é necessária. Uma análise de desempenho pode ajudar a identificar se as válvulas estão permitindo o fluxo e a pressão adequados. Uma abordagem proativa pode evitar problemas maiores que podem surgir no futuro, garantindo a operação otimizada de todo o sistema.
Em suma, reconhecer os sinais que indicam a necessidade de calibração das válvulas é essencial para manter a eficiência e a segurança dos sistemas. Esteja ciente dos vazamentos, mudanças de desempenho, leituras de pressão flutuantes, ciclos de operação imprecisos, temperaturas inconsistente, ruídos anormais e a falta de manutenção. Cada um desses indicadores pode ser um aviso para realizar uma calibração, evitando assim falhas dispendiosas e perigosas no sistema. Manter práticas de manutenção contínua e uma vigilância atenta é a melhor abordagem para garantir que suas válvulas estejam sempre operando em suas melhores condições.
Fatores que Afetam a Calibração de Válvulas
A calibração de válvulas é um processo crítico que assegura que esses componentes desempenhem seu papel de maneira eficaz em sistemas industriais e comerciais. No entanto, vários fatores podem influenciar a precisão e a eficácia da calibração. Compreender esses fatores é fundamental para garantir que as válvulas operem dentro das especificações e para evitar falhas que possam comprometer todo o sistema. Neste artigo, exploraremos os principais fatores que afetam a calibração de válvulas e como mitigá-los.
Um dos fatores mais significativos que podem afetar a calibração é a escolha inadequada do equipamento. Válvulas diferentes têm necessidades específicas de calibração, e o uso do equipamento incorreto pode resultar em medições imprecisas. Por exemplo, um manômetro que não esteja com a classificação adequada para a pressão que a válvula opera pode levar a leituras erradas. Portanto, é essencial selecionar o equipamento de calibração apropriado, levando em consideração as especificações da válvula e as condições do sistema.
Além da escolha do equipamento, a qualidade do próprio manômetro ou calibrador pode impactar diretamente a calibração. Instrumentos de baixa qualidade podem ter margens de erro maiores e, consequentemente, comprometer a precisão das medições. Garantir que todos os instrumentos utilizados sejam calibrados e de alta qualidade é essencial para a obtenção de resultados confiáveis. Algumas indústrias optam por implementar um cronograma regular de calibração de seus instrumentos para garantir que estejam sempre dentro de especificações rigorosas.
Outro fator que pode afetar a calibração de válvulas é a temperatura e a pressão do fluido que está sendo trabalhado. Válvulas podem ter desempenho diferente sob condições variadas de temperatura e pressão, alterando assim as leituras e a calibração. Por exemplo, uma válvula que é calibrada a uma temperatura ambiente pode não funcionar da mesma forma quando o fluido estiver a temperaturas elevadas. Portanto, ao realizar a calibração, é crucial simular as condições reais de operação para obter resultados mais precisos.
A contaminação do fluido é outro aspecto que pode afetar negativamente a calibração das válvulas. Impurezas ou resíduos dentro do sistema podem interferir na operação da válvula, limitando sua capacidade de abrir e fechar corretamente. Isso, por sua vez, pode levar a medições erradas durante a calibração. Portanto, é fundamental que o sistema seja mantido limpo e livre de contaminantes. A manutenção regular, incluindo a filtragem do fluido, pode ajudar a minimizar esses impactos e garantir uma calibração mais eficaz.
O desgaste mecânico da válvula é um fator frequentemente negligenciado, mas que pode ter um grande efeito na calibração. Com o tempo, as válvulas podem sofrer desgastes, corrosão ou danos devido à pressão e ao fluxo contínuo do fluido. Esses problemas podem resultar em desvios nas medições e na necessidade de recalibrações mais frequentes. Portanto, inspecionar regularmente as válvulas e substituí-las quando necessário é fundamental para manter a eficiência do sistema.
A correta instalação da válvula também é um fator que pode impactar a calibração. Válvulas que não foram instaladas corretamente podem apresentar dificuldades na operação, resultando em medições imprecisas. É crucial que a instalação seja feita de acordo com as especificações do fabricante e que os procedimentos corretos sejam seguidos durante a instalação. Falhas na instalação podem levar a problemas de alinhamento e restrições ao fluxo, prejudicando o desempenho da válvula.
Além disso, a falta de treinamento adequado para os operadores responsáveis pela calibração pode influenciar negativamente o processo. Profissionais que não estão suficientemente treinados podem cometer erros ao realizar medições e ajustes, levando a uma calibração imprecisa. Portanto, é essencial que os operadores recebam formação e instruções adequadas para garantir que a calibração seja realizada de maneira correta e eficaz.
A frequência das calibrações também desempenha um papel na eficácia do processo. Calibrar as válvulas apenas em longos intervalos pode resultar em desvio significativo, tornando o processo de calibração mais difícil e menos eficaz. Implementar um cronograma regular de calibração, de acordo com a recomendação do fabricante e as necessidades específicas do sistema, ajudará a garantir que as válvulas permaneçam operando dentro dos parâmetros desejados.
Por fim, as condições ambientais, como umidade e temperatura do ambiente, podem afetar o desempenho dos instrumentos de calibração e das válvulas. Ambientes extremos podem causar dilatações ou contrações nos materiais, ou até mesmo danificá-los. Certifique-se de que o local onde as válvulas estão instaladas e calibradas seja adequado para o funcionamento ideal dos equipamentos.
Em resumo, entender os fatores que afetam a calibração de válvulas permite a implementação de estratégias eficazes para evitar falhas operacionais e melhorar o desempenho dos sistemas industriais. Desde a escolha do equipamento até as condições de instalação e ambiente, cada um desses fatores desempenha um papel importante na eficácia da calibração. Mantenha testados protótipos em boas condições, execute manutenções regulares e garanta que todos os profissionais estejam adequadamente treinados para realizar calibrações precisas e confiáveis.
Manutenção Pós-Calibração e Dicas
A calibração de válvulas é um aspecto crucial para garantir a eficiência e a segurança nos sistemas industriais. No entanto, a calibração por si só não é suficiente; a manutenção pós-calibração é igualmente importante para assegurar que as válvulas continuem a operar de forma eficaz ao longo do tempo. Neste artigo, abordaremos a importância da manutenção pós-calibração e forneceremos dicas valiosas para manter suas válvulas em perfeito estado.
Após a calibração, o primeiro passo a ser seguido é realizar uma verificação completa do sistema. Isso envolve monitorar o desempenho das válvulas em operação normal e garantir que estejam funcionando de acordo com as especificações estabelecidas. Acompanhe as medições de pressão e fluxo para identificar quaisquer anomalias que possam surgir imediatamente após a calibração. A detecção precoce de problemas pode evitar falhas maiores e custos desnecessários.
Um ponto importante na manutenção pós-calibração é a documentação. É fundamental registrar todos os resultados da calibração, incluindo as medições realizadas, os ajustes feitos e as condições de operação durante o processo. Essa documentação é crucial para futuras referências e para manter um histórico de manutenções e calibrações em seus sistemas. Além disso, ao manter registros detalhados, você poderá identificar padrões e tendências que poderão contribuir para um melhor planejamento nas manutenções futuras.
Outro aspecto relevante é o treinamento contínuo da equipe responsável pela operação e manutenção das válvulas. As mudanças nas tecnologias e nas melhores práticas exigem que os operadores sejam mantidos atualizados sobre novos procedimentos e equipamentos. Investir em formação regular pode garantir que todos estejam cientes das práticas de manutenção adequadas e que compreendam a importância de seguir as recomendações do fabricante parao manuseio e calibração das válvulas.
Afrequentemente negligenciada, a limpeza das válvulas também é um passo importante na manutenção pós-calibração. O acúmulo de sujeira, resíduos ou outros contaminantes pode afetar a operação da válvula, levando à perda de precisão nas medições e no controle do fluxo. Crie um cronograma regular para limpeza e inspeção das válvulas, garantindo que os componentes estejam limpos e prontos para operação. Medidas defensivas como a instalação de filtros podem também ser implementadas para proteger as válvulas e minimizar a poluição.
Outro ponto que merece atenção é a verificação das conexões e componentes adjacentes. Certifique-se de que todas as conexões estão firmes e livres de vazamentos. Um sistema interligado pode funcionar apenas tão bem quanto o seu componente mais fraco. Inspecione não apenas as válvulas, mas também os tubos, mangueiras e conexões que fazem parte do sistema. A detecção e reparo antecipado de vazamentos podem economizar tempo e custos com manutenções mais extensas no futuro.
É recomendável realizar um monitoramento contínuo das válvulas após a calibração. Muitos sistemas modernos de automação permitem o uso de tecnologia para monitorar o desempenho das válvulas em tempo real. Esse monitoramento pode incluir o uso de sensores que detectam mudanças de pressão e fluxo, permitindo a identificação imediata de quaisquer desvios das especificações. O uso dessa tecnologia pode facilitar a manutenção preventiva e correções rápidas, contribuindo para a eficácia do sistema como um todo.
Outra dica valiosa é estabelecer um cronograma regular de manutenção e revisão. Mesmo que as válvulas tenham sido calibradas recentemente, um programa de manutenção preventiva ajudará a identificar quaisquer problemas antes que eles afetem o desempenho. Estabeleça um plano de manutenção que inclua a frequência das inspeções e calibrações, e desenvolva uma lista de pontos a serem verificados durante cada visita de manutenção. Esse tipo de planejamento ajudará a garantir que os sistemas continuem a funcionar sem interrupções.
A escolha de fornecedores de qualidade para a aquisição de válvulas e componentes é outra estratégia essencial. Um usado de baixa qualidade pode não funcionar de acordo com as especificações, exigindo mais manutenções e calibrações frequentes. Ao selecionar fornecedores que se destacam pela qualidade e pelo suporte ao cliente, você estará investindo em um sistema menos propenso a falhas, economizando em custos de manutenção e munido de um suporte confiável.
Por último, envolva sua equipe em um diálogo contínuo sobre melhorias e inovações. O feedback dos operadores que utilizam as válvulas diariamente pode ser valioso para identificar problemas ou áreas que necessitam de melhorias. Organize reuniões regulares onde a equipe possa discutir suas experiências e sugerir mudanças que podem aumentar a eficiência das válvulas e do sistema como um todo.
Em suma, a manutenção pós-calibração é uma etapa vital para garantir que suas válvulas continuem a operar de forma eficaz. A documentação rigorosa, a limpeza regular, o monitoramento contínuo, além de um ciclo de manutenção programado são práticas que minimizam falhas e aumentam a eficiência do sistema. Implementar essas dicas não apenas prolongará a vida útil de suas válvulas, mas também contribuirá para a segurança e lucratividade das operações. Ao investir tempo e recursos na manutenção adequada, você perceberá índices de eficiência e operacionais muito superiores.
Erros Comuns na Calibração de Válvulas e Como Evitá-los
A calibração de válvulas é uma parte crítica da manutenção na indústria, garantindo que os sistemas operem de forma eficiente e segura. No entanto, como em qualquer processo técnico, existem erros comuns que podem comprometer a eficácia da calibração. Entender esses erros e como evitá-los é fundamental para garantir um desempenho ideal das válvulas e, consequentemente, de todo o sistema. Neste artigo, discutiremos os erros mais frequentes na calibração de válvulas e forneceremos dicas sobre como evitá-los.
Um dos erros mais comuns é a falta de planejamento adequado antes de iniciar o processo de calibração. Muitas vezes, os técnicos começam a calibração sem revisar as especificações do fabricante ou as condições de operação. Isso pode levar a ajustes inadequados e resultados imprecisos. Para evitar esse erro, sempre tenha em mãos a documentação técnica da válvula, incluindo as recomendações do fabricante sobre os parâmetros e as condições de calibração. Preparar um checklist antes de iniciar o processo pode ajudar na organização e na eficácia do procedimento.
Outro erro frequente é o uso de equipamentos de calibração inadequados ou não calibrados. A precisão em medições é essencial para garantir resultados confiáveis na calibração. Instrumentos de medição que não foram calibrados ou que não possuem a sensibilidade adequada podem resultar em medições erradas. Para evitar esse problema, assegure-se de que todos os equipamentos utilizados, como manômetros e calibradores, estejam devidamente calibrados e em bom estado de funcionamento. Além disso, use instrumentos que sejam apropriados para as especificações da válvula em questão.
A falta de treinamento adequado dos profissionais responsáveis pela calibração também é uma armadilha comum. Técnicos não treinados podem cometer erros durante o processo, como não entender como interpretar as leituras de pressão ou não aplicar as técnicas corretas de ajuste. Para evitar que isso aconteça, invista em treinamentos regulares e atualizações para sua equipe. Um operador bem treinado terá confiança e conhecimento suficientes para executar a calibração de forma eficaz.
A realização de calibrações em condições inadequadas é outro erro que pode comprometer a precisão do processo. Por exemplo, a calibração em temperaturas extremas ou em condições de alta umidade pode impactar as medições e a operação da válvula. É crucial que o processo de calibração seja realizado dentro das faixas de temperatura e outras condições ambientais recomendadas pelo fabricante. Se o ambiente não for adequado, considere adiar o processo até que as condições sejam mais favoráveis.
A negligência na verificação do estado da válvula antes da calibração pode levar a erros significativos. Se uma válvula estiver danificada, desgastada ou entupida, isso pode afetar sua capacidade de operar corretamente, mesmo após a calibração. Sempre faça uma inspeção visual detalhada antes de realizar a calibração. Verifique se há sinais de desgaste, corrosão ou obstruções, e resolva quaisquer problemas antes de ajustar a válvula.
A falta de registro e documentação dos resultados da calibração é um erro que pode prejudicar a eficácia do gerenciamento de manutenção. Ao não registrar as medições e ajustes realizados, você pode perder a capacidade de rastrear a performance da válvula ao longo do tempo. Isso pode levar a repetições desnecessárias de calibrações. Para evitar esse erro, crie um protocolo de documentação que inclua todos os dados relevantes durante o processo de calibração, garantindo que as informações possam ser facilmente acessadas no futuro.
O não cumprimento de um cronograma de calibração regular é um erro que pode resultar em problemas recorrentes. Algumas empresas só realizam calibrações quando percebem problemas, o que pode ser muito tarde. Para evitar essa situação, estabeleça um cronograma regular de calibração com base nas recomendações do fabricante e nas necessidades específicas do sistema. Realizar calibrações preventivas pode ajudar a identificar problemas antes que se tornem críticos.
Além disso, não considerar as interações entre diferentes válvulas e sistemas ao calibrar pode levar a problemas maiores. Muitas vezes, as válvulas não operam isoladamente, e alterações em uma válvula podem afetar outras partes do sistema. É importante ter uma visão holística do sistema e, sempre que possível, calibrar válvulas em conjunto ou considerar como as alterações em uma válvula podem impactar o desempenho geral. Isso ajuda a garantir um funcionamento harmonioso de todo o sistema.
Por último, nunca subestime a importância da manutenção pós-calibração. Uma vez que a válvula foi calibrada, é crucial continuar monitorando seu desempenho. Ignorar o acompanhamento pode resultar em um retorno a condições de operação inadequadas. Para evitar isso, implemente um sistema de monitoramento contínuo do desempenho da válvula, registrando indicadores-chave que possam sinalizar a necessidade de futuras calibrações.
Em conclusão, a calibração de válvulas é um processo complexo que pode ser comprometido por vários erros comuns. Ao entender e evitar esses erros, você pode garantir que suas válvulas operem de maneira eficiente e segura. O planejamento adequado, o uso correto de equipamentos, o treinamento de sua equipe e a atenção às condições de operação são passos fundamentais para evitar erros e garantir a eficácia das calibrações. Com uma abordagem proativa e cuidadosa, sua manutenção de válvulas poderá levar a operações contínuas e eficientes, maximizando a segurança e a produtividade do seu sistema industrial.
Em resumo, a calibração de válvulas é um procedimento essencial que não apenas assegura a eficiência e a segurança dos sistemas, mas também prolonga a vida útil dos equipamentos. Ao longo deste artigo, abordamos a importância da calibração, os diferentes tipos de válvulas, e os erros comuns que podem ser cometidos durante o processo, bem como dicas práticas para evitar esses erros. Com o conhecimento adquirido sobre a manutenção adequada e os fatores que influenciam a calibração, você estará mais preparado para garantir o desempenho ideal das válvulas em suas operações. A implementação de práticas de calibração sistemáticas pode resultar em aumentos significativos na eficiência operacional, redução de custos de manutenção e um ambiente de trabalho mais seguro. Portanto, não subestime a importância da calibração de válvulas: faça dela uma prioridade em sua rotina de manutenção e veja os benefícios se concretizarem em suas operações.