Calibração de Válvulas de Segurança: Guia Completo e Importância
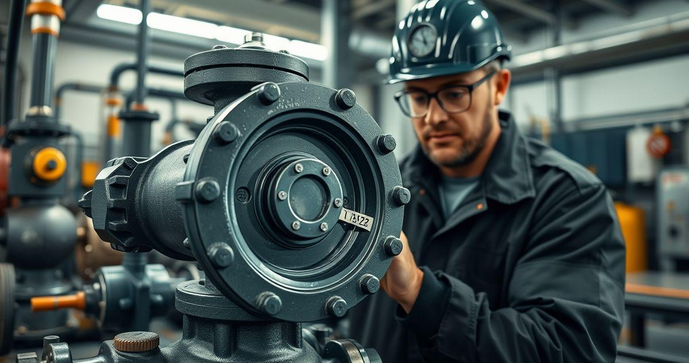
Por: Lucas - 17 de Abril de 2025
Importância da Calibração de Válvulas de Segurança para a Indústria
A calibração de válvulas de segurança é fundamental para garantir a integridade e a segurança dos sistemas industriais. Essas válvulas são projetadas para liberar pressão excessiva em equipamentos e tubulações, evitando acidentes graves e danos ao patrimônio.A ausência de calibração pode resultar em falhas que levam a explosões ou vazamentos químicos.
Além da prevenção de acidentes, a calibração regular das válvulas assegura que elas respondam corretamente sob condições extremas. Isso é essencial em indústrias como a petroquímica, onde a pressão pode variar rapidamente e impactar a operação.Um sistema em que as válvulas estão corretamente calibradas opera de maneira mais eficiente, contribuindo para a produtividade.
Outro aspecto crucial é a conformidade com as normas de segurança. Muitas regulamentações exigem que as válvulas de segurança sejam calibradas em intervalos determinados para assegurar a confiança no funcionamento do equipamento.Seguir essas diretrizes reduz o risco de multas e penalidades legais, além de promover um ambiente de trabalho seguro.
A calibração também desempenha um papel significativo na manutenção preventiva. Com a calibração regular, é possível identificar desgastes e possíveis falhas nas válvulas antes que se tornem problemas maiores, resultando em menores custos com reparos.Isso proporciona uma operação contínua e segura, minimizando o tempo de inatividade.
Por fim, um bom programa de calibração contribui para a confiança dos funcionários nas operações. Saber que os sistemas estão sendo monitorados e mantidos corretamente promove um ambiente de trabalho mais seguro e produtivo.A segurança do trabalhador deve ser a prioridade de qualquer operação industrial.
Procedimentos de Calibração: Passo a Passo
O primeiro passo para a calibração de válvulas de segurança é revisar a documentação do fabricante. É essencial entender as especificações e os requisitos do modelo específico que será calibrado.A documentação fornece informações vitais sobre pressões de teste e procedimentos recomendados.
Após a revisão, o próximo passo é preparar o equipamento e o local de teste. Isso inclui a verificação de ferramentas necessárias, como manômetros calibrados e dispositivos de teste, além de garantir que a área esteja livre de riscos.Um ambiente seguro e organizado é crucial para a realização de uma calibração eficiente.
O processo começa com a instalação do manômetro na válvula de segurança. O manômetro deve ser calibrado e ter uma faixa de medição que atenda à pressão de operação da válvula.A instalação correta do manômetro é fundamental para uma calibração precisa.
Em seguida, a válvula deve ser submetida a um teste de pressão que aumentará gradualmente até atingir o ponto de abertura da válvula. Este ponto deve ser monitorado de perto para garantir que a válvula se abra na pressão especificada pelo fabricante.Se a válvula não abrir na pressão correta, ajustes devem ser realizados.
Após o teste de abertura, é importante também testar o fechamento da válvula. Isso é feito reduzindo lentamente a pressão até que a válvula se feche completamente. Este procedimento garante que a válvula opere corretamente em ambas as direções.Um retorno correto ao estado fechado é essencial para a segurança do sistema.
Por fim, após a calibração, deve-se registrar todos os dados e observações em um relatório detalhado. Isso inclui a pressão de abertura e fechamento, quaisquer ajustes realizados e as condições durante o teste.Um registro adequado contribui para a manutenção contínua e a conformidade normativa.
Normas e Regulamentações Relacionadas à Calibração
As normas e regulamentações relacionadas à calibração de válvulas de segurança visam garantir a segurança e a eficiência operacional nas indústrias. Diversas organizações, como a American Society of Mechanical Engineers (ASME) e a International Organization for Standardization (ISO), estabelecem diretrizes que devem ser seguidas. Essas normas garantem que as válvulas funcionem conforme projetado e contribuam para a segurança dos trabalhadores.
Uma das principais normas é a ASME PTC 25, que trata especificamente sobre a calibração de válvulas de segurança e alívio. Ela fornece orientações sobre os métodos de teste e os intervalos recomendados para calibração, com foco na segurança e na confiabilidade do equipamento. Seguir essas orientações ajudam a prevenir acidentes e a aumentar a durabilidade das válvulas.
Além da ASME, a norma ISO 9001 também é relevante, pois abrange o gerenciamento da qualidade em processos industriais. Empresas que implementam essa norma são incentivadas a desenvolver programas de manutenção e calibração que atendam a requisitos de segurança e qualidade. A certificação ISO pode melhorar a imagem da empresa e garantir a conformidade com padrões globais.
As regulamentações locais e nacionais também desempenham um papel importante. Muitas jurisdições exigem que empresas realizem calibrações em intervalos específicos, documentadas de acordo com as normas da indústria. Produtos que não atendem a esses requisitos podem resultar em multas e paralisações. A conformidade com as regulamentações locais não só evita penalidades, mas também assegura a segurança operacional.
Por fim, a formação e capacitação dos profissionais envolvidos na calibração são igualmente criticamente importantes. As organizações devem garantir que seus técnicos estejam cientes das normas e regulamentos vigentes, proporcionando treinamentos adequados para a sua equipe. Um pessoal qualificado é fundamental para a realização de calibrações precisas e seguras.
Fatores que Afetam a Calibração de Válvulas
Diversos fatores podem influenciar a calibração de válvulas de segurança, impactando sua eficiência e funcionalidade. Um dos principais fatores é a pressão de operação do sistema. As válvulas devem ser calibradas considerando a pressão máxima e mínima que podem enfrentar, garantindo que funcionem adequadamente nessas condições.Uma calibração que não considera esses limites pode resultar em falhas de funcionamento.
Outro aspecto a ser considerado é a temperatura do ambiente em que a válvula está instalada. Temperaturas extremas podem afetar a performance dos materiais utilizados na válvula, influenciando sua capacidade de abrir e fechar em pressões específicas.Manter a temperatura dentro de níveis recomendados é essencial para garantir a segurança do sistema.
A qualidade dos materiais utilizados na construção da válvula também é um fator determinante. Válvulas fabricadas com materiais inferiores podem sofrer desgastes mais rapidamente e, portanto, necessitar de calibrações mais frequentes para manter seu desempenho.Investir em válvulas de alta qualidade diminui a frequência de manutenção.
A ocorrência de corrosão ou acúmulo de sujeira na válvula pode comprometer sua operação. Elementos químicos, especialmente em indústrias químicas e petroquímicas, podem agravar o desgaste e a obstrução, dificultando o movimento da válvula e afetando a calibração.Implementar limpeza e manutenção regulares é crucial para evitar esses problemas.
Por fim, a falta de manutenção preventiva pode levar a resultados imprecisos na calibração. Um programa de manutenção que inclui inspeções regulares e a verificação de lubrificação é vital para garantir que a válvula permaneça em boas condições de funcionamento e atenda aos padrões de segurança.A manutenção adequada é a chave para prolongar a vida útil da válvula e melhorar sua eficiência.
Ferramentas e Equipamentos Necessários para Calibração
Para realizar a calibração de válvulas de segurança de forma eficaz, é fundamental dispor das ferramentas e equipamentos corretos. Um dos principais itens necessários é o manômetro calibrado, que mede com precisão a pressão no sistema. Um manômetro de qualidade garante leituras confiáveis e precisas durante o processo de calibração.
Além do manômetro, é importante ter uma fonte de pressão calibrada, que permite aumentar gradualmente a pressão até o nível especificado para teste da válvula. Essa fonte deve ser confiável e capaz de suportar a faixa de pressão necessária. A precisão na fonte de pressão é crucial para evitar erros durante os testes.
Um suporte adequado para montagem do manômetro e outros acessórios de teste garante estabilidade e segurança durante o processo de calibração. Um suporte bem posicionado ajuda a evitar vazamentos e facilita o acesso às válvulas. Um bom suporte contribui para a eficiência do teste e a segurança do operador.
Ferramentas de ajuste, como chaves inglesas e chave de fenda, são necessárias para realizar as modificações nas válvulas durante o processo de calibração. Elas devem ser adequadas ao tipo de válvula e aos requisitos de torque especificados pelo fabricante. Utilizar a ferramenta correta evita danos às válvulas e assegura o ajuste adequado.
Por último, mas não menos importante, equipamentos de proteção individual (EPIs) são essenciais durante a calibração. Isso inclui óculos de segurança, luvas e protetores auditivos, dependendo do ambiente de trabalho e das especificações de segurança da indústria. A utilização de EPIs é fundamental para garantir a segurança do técnico durante a calibração.
Benefícios da Calibração Regular para a Segurança Operacional
A calibração regular de válvulas de segurança traz uma série de benefícios significativos para a segurança operacional nas indústrias. Um dos principais benefícios é a prevenção de acidentes. Com a calibração adequada, as válvulas funcionam como projetadas, minimizando o risco de falhas que podem resultar em explosões ou vazamentos graves.A manutenção preventiva desenvolve um ambiente de trabalho mais seguro para todos os colaboradores.
Outro benefício crucial é a conformidade com normas e regulamentações de segurança. Muitas organizações e agências governamentais exigem que a calibração de válvulas de segurança seja realizada em intervalos específicos. Assim, a calibração regular ajuda a garantir que a empresa cumpra com as regulamentações, evitando multas e penalidades.Estar em conformidade não apenas protege a empresa legalmente, mas também promove uma cultura de segurança.
A calibração regular também contribui para a otimização dos processos operacionais. Válvulas que funcionam corretamente mantêm a pressão adequada no sistema, o que melhora a eficiência do equipamento e reduz o tempo de inatividade. Isso significa uma produção mais eficaz e menos desperdício de recursos.Aumentar a eficiência operacional resulta em custos reduzidos e maior produtividade.
Além disso, a calibração frequente facilita a identificação de possíveis problemas antes que se tornem sérios. Durante o processo de calibração, desgastes e falhas podem ser detectados, permitindo a realização de reparos ou substituições a tempo, evitando interrupções inesperadas na operação.A detecção precoce de falhas minimiza os custos com manutenção e aumenta a vida útil das válvulas.
Por fim, a segurança e a confiança dos funcionários aumentam quando eles sabem que o sistema está sendo monitorado e calibrado regularmente. Isso promove um ambiente de trabalho mais positivo, onde os colaboradores se sentem valorizados e protegidos.Um espaço de trabalho seguro e eficiente é crucial para a retenção de talentos e satisfação dos colaboradores.
A calibração de válvulas de segurança é uma prática indispensável para garantir a segurança e a eficiência operacional nas indústrias. Desde a prevenção de acidentes até a conformidade com normas e regulamentações, seus benefícios são significativos.
Investir em calibração regular não apenas melhora a segurança, mas também otimiza processos e prolonga a vida útil dos equipamentos.
Através de procedimentos adequados, utilização de ferramentas corretas e um acompanhamento constante, as empresas podem assegurar que suas válvulas operem de maneira confiável e segura. Além disso, isso promove um ambiente de trabalho mais positivo e produtivo.
Portanto, priorizar a calibração é essencial para qualquer organização que deseje manter altos padrões de segurança e eficiência.