Calibração de Válvulas: Importância e Passo a Passo para um Desempenho Eficiente
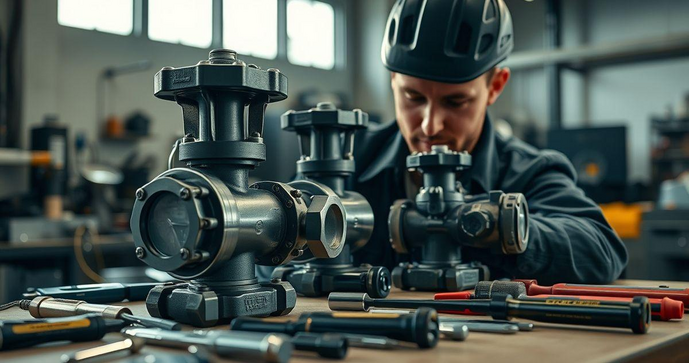
Por: Lucas - 26 de Janeiro de 2025
A calibração de válvulas é um processo fundamental para garantir o desempenho eficiente e seguro de sistemas industriais. Com o aumento da complexidade das operações e a necessidade de precisão, a calibração adequada se torna essencial para evitar falhas e otimizar o funcionamento dos equipamentos. Neste artigo, abordaremos a importância da calibração de válvulas, o passo a passo para realizá-la corretamente, além de discutir erros comuns e práticas de manutenção pós-calibração.
Importância da Calibração de Válvulas na Indústria
A calibração de válvulas é um aspecto crucial na operação de sistemas industriais, desempenhando um papel vital na eficiência e segurança das operações. As válvulas são componentes essenciais em diversos processos, controlando o fluxo de líquidos e gases em tubulações. Quando não calibradas corretamente, podem resultar em sérios problemas, como vazamentos, falhas de equipamento e até mesmo acidentes industriais. Portanto, entender a importância da calibração de válvulas é fundamental para qualquer profissional que atua na área industrial.
Um dos principais motivos para a calibração de válvulas é garantir a precisão no controle de fluxo. Em muitos processos industriais, a quantidade de fluido que passa por uma válvula deve ser monitorada e ajustada com precisão. Isso é especialmente importante em indústrias químicas e petroquímicas, onde a mistura de substâncias deve ser exata para evitar reações indesejadas. A calibração adequada assegura que as válvulas operem dentro das especificações, minimizando o risco de erros que podem comprometer a qualidade do produto final.
Além disso, a calibração de válvulas contribui para a eficiência energética. Válvulas mal calibradas podem causar desperdício de energia, uma vez que podem permitir o fluxo excessivo de fluidos, resultando em maior consumo de energia para manter a pressão e o fluxo desejados. Ao calibrar as válvulas corretamente, as indústrias podem otimizar o uso de energia, reduzindo custos operacionais e contribuindo para práticas mais sustentáveis.
A segurança é outro fator crítico que destaca a importância da calibração de válvulas. Em ambientes industriais, a falha de uma válvula pode levar a situações perigosas, como explosões ou vazamentos de substâncias tóxicas. A calibração regular ajuda a identificar e corrigir problemas antes que se tornem críticos, garantindo que as válvulas funcionem de maneira confiável. Isso é especialmente relevante em indústrias que lidam com produtos químicos perigosos ou gases inflamáveis, onde a segurança dos trabalhadores e do ambiente é uma prioridade.
Além disso, a calibração de válvulas pode prolongar a vida útil dos equipamentos. Válvulas que não estão calibradas corretamente podem sofrer desgaste prematuro devido ao funcionamento inadequado. Isso pode resultar em custos elevados com manutenção e substituição de peças. Ao realizar a calibração regularmente, as indústrias podem evitar esses problemas, garantindo que as válvulas operem de maneira eficiente e duradoura.
Outro aspecto importante é a conformidade com normas e regulamentos. Muitas indústrias são obrigadas a seguir padrões específicos de segurança e qualidade, que incluem a calibração de válvulas. A não conformidade pode resultar em penalidades financeiras e danos à reputação da empresa. Portanto, a calibração não é apenas uma prática recomendada, mas muitas vezes uma exigência legal que deve ser atendida para garantir a operação segura e eficiente das instalações.
Além disso, a calibração de válvulas está intimamente relacionada ao desempenho de outros equipamentos industriais, como o Pressostato industrial. Esses dispositivos trabalham em conjunto com as válvulas para monitorar e controlar a pressão em sistemas de tubulação. Se as válvulas não estiverem calibradas corretamente, o pressostato pode não funcionar de maneira eficaz, resultando em falhas no sistema. Portanto, a calibração de válvulas deve ser vista como parte de um sistema integrado de controle e monitoramento, onde cada componente desempenha um papel vital na operação geral.
Por fim, a calibração de válvulas é uma prática que deve ser realizada por profissionais qualificados, que compreendam as especificações técnicas e os requisitos de cada tipo de válvula. A calibração inadequada pode levar a resultados imprecisos e até mesmo danificar os equipamentos. Portanto, investir em treinamento e capacitação para a equipe responsável pela calibração é essencial para garantir que as válvulas operem de maneira eficiente e segura.
Em resumo, a calibração de válvulas na indústria é de extrema importância, pois garante precisão no controle de fluxo, eficiência energética, segurança, prolonga a vida útil dos equipamentos e assegura a conformidade com normas e regulamentos. Com a crescente complexidade dos processos industriais, a calibração adequada se torna uma prática indispensável para garantir operações seguras e eficientes.
Passo a Passo para Realizar a Calibração de Válvulas
Realizar a calibração de válvulas é um processo essencial para garantir o funcionamento eficiente e seguro de sistemas industriais. A calibração adequada assegura que as válvulas operem dentro das especificações desejadas, evitando problemas como vazamentos e falhas no controle de fluxo. A seguir, apresentamos um passo a passo detalhado para realizar a calibração de válvulas de forma eficaz.
O primeiro passo na calibração de válvulas é a preparação do ambiente de trabalho. Antes de iniciar o processo, é fundamental garantir que a área esteja limpa e organizada. Remova qualquer obstrução que possa interferir na calibração e certifique-se de que todas as ferramentas necessárias estejam disponíveis. Isso inclui manômetros, chaves de fenda, chaves inglesas, e, se necessário, um Válvula solenoide para água para controle adicional do fluxo. A segurança deve ser a prioridade, então use equipamentos de proteção individual, como luvas e óculos de segurança.
Após a preparação do ambiente, o próximo passo é desligar o sistema. Isso é crucial para evitar acidentes durante a calibração. Desconecte a fonte de energia e feche as válvulas de entrada e saída do sistema. Certifique-se de que não haja pressão residual nas tubulações antes de prosseguir. A segurança é fundamental, e trabalhar com válvulas sob pressão pode ser extremamente perigoso.
Com o sistema desligado e seguro, é hora de inspecionar a válvula. Verifique se há sinais de desgaste, corrosão ou danos visíveis. Se a válvula estiver em más condições, pode ser necessário realizar reparos ou substituições antes de proceder com a calibração. Uma válvula danificada pode comprometer a precisão da calibração e afetar o desempenho do sistema.
O próximo passo é conectar o manômetro à válvula. O manômetro é um instrumento que mede a pressão do fluido que passa pela válvula. Conecte-o de acordo com as instruções do fabricante, garantindo que todas as conexões estejam firmes e seguras. Isso garantirá leituras precisas durante o processo de calibração.
Uma vez que o manômetro esteja instalado, é hora de abrir lentamente a válvula. Isso deve ser feito de forma gradual para evitar picos de pressão que possam danificar o sistema. Observe as leituras do manômetro enquanto a válvula é aberta. O objetivo é ajustar a válvula para que ela opere dentro das especificações desejadas, que podem variar dependendo do tipo de válvula e do sistema em que está instalada.
Durante a abertura da válvula, preste atenção às leituras do manômetro. Se a pressão estiver abaixo do esperado, pode ser necessário ajustar a válvula. Isso pode ser feito girando o parafuso de ajuste ou a alavanca, dependendo do tipo de válvula. Siga as instruções do fabricante para garantir que os ajustes sejam feitos corretamente. O ideal é que a válvula atinja a pressão desejada sem oscilações significativas.
Após realizar os ajustes necessários, feche a válvula novamente e desconecte o manômetro. É importante realizar um teste final para garantir que a calibração foi bem-sucedida. Abra a válvula uma última vez e observe as leituras do manômetro. Se a pressão estiver dentro das especificações desejadas, a calibração foi realizada com sucesso. Caso contrário, pode ser necessário repetir o processo de ajuste até que os resultados sejam satisfatórios.
Uma vez que a calibração esteja concluída, é fundamental documentar o processo. Registre as leituras iniciais e finais, bem como quaisquer ajustes realizados. Essa documentação é importante para futuras referências e para garantir a conformidade com as normas e regulamentos da indústria. Além disso, a documentação pode ser útil para identificar padrões de desempenho ao longo do tempo, permitindo que você faça ajustes proativos quando necessário.
Por fim, após a calibração, é recomendável realizar uma verificação regular das válvulas. A calibração não é um processo único; as válvulas devem ser monitoradas e recalibradas periodicamente para garantir que continuem a operar de maneira eficiente. A frequência da calibração pode variar dependendo do tipo de válvula, do ambiente de operação e da criticidade do sistema. Estabelecer um cronograma de manutenção preventiva ajudará a evitar problemas futuros e a garantir a segurança e eficiência do sistema.
Em resumo, a calibração de válvulas é um processo essencial que envolve várias etapas, desde a preparação do ambiente até a documentação dos resultados. Seguir este passo a passo garantirá que as válvulas operem de maneira eficiente e segura, contribuindo para o desempenho geral do sistema industrial. A calibração adequada não apenas melhora a eficiência, mas também prolonga a vida útil dos equipamentos e assegura a conformidade com as normas de segurança.
Erros Comuns na Calibração de Válvulas e Como Evitá-los
A calibração de válvulas é um processo crítico para garantir a eficiência e a segurança em sistemas industriais. No entanto, existem diversos erros que podem ocorrer durante esse processo, comprometendo o desempenho das válvulas e, consequentemente, a operação do sistema. Neste artigo, abordaremos os erros comuns na calibração de válvulas e como evitá-los, garantindo que o processo seja realizado de forma eficaz.
Um dos erros mais frequentes na calibração de válvulas é a falta de preparação adequada do ambiente de trabalho. Muitas vezes, os profissionais iniciam o processo sem garantir que a área esteja limpa e organizada. Isso pode levar a distrações e, em última instância, a erros durante a calibração. Para evitar esse problema, é fundamental dedicar tempo à preparação do local, removendo obstruções e garantindo que todas as ferramentas necessárias estejam à mão. Além disso, o uso de equipamentos de proteção individual (EPIs) é essencial para garantir a segurança durante o processo.
Outro erro comum é a falta de desconexão da fonte de energia antes de iniciar a calibração. Trabalhar com válvulas sob pressão pode ser extremamente perigoso, e a falta de atenção a esse detalhe pode resultar em acidentes graves. Para evitar esse erro, sempre verifique se a fonte de energia está desconectada e se as válvulas de entrada e saída estão fechadas antes de iniciar o processo de calibração. A segurança deve ser a prioridade máxima em qualquer operação industrial.
Além disso, muitos profissionais cometem o erro de não inspecionar a válvula antes de calibrá-la. A inspeção é uma etapa crucial que permite identificar sinais de desgaste, corrosão ou danos visíveis. Ignorar essa etapa pode resultar em calibrações imprecisas e até mesmo em falhas no sistema. Portanto, sempre realize uma inspeção minuciosa da válvula antes de iniciar a calibração. Se a válvula estiver em más condições, pode ser necessário realizar reparos ou substituições antes de prosseguir.
Outro erro comum é a falta de uso de instrumentos de medição adequados. A calibração de válvulas requer o uso de manômetros e outros dispositivos de medição para garantir que as leituras sejam precisas. Utilizar instrumentos inadequados ou com calibração desatualizada pode levar a resultados imprecisos. Para evitar esse problema, sempre verifique se os instrumentos de medição estão em boas condições e calibrados corretamente antes de iniciar o processo. Isso garantirá que as leituras sejam confiáveis e que a calibração seja realizada de forma eficaz.
Durante o processo de calibração, é comum que os profissionais não sigam as instruções do fabricante. Cada tipo de válvula pode ter especificações e procedimentos de calibração diferentes, e ignorar essas diretrizes pode resultar em erros significativos. Para evitar esse problema, sempre consulte o manual do fabricante e siga as instruções cuidadosamente. Isso garantirá que a calibração seja realizada de acordo com as especificações corretas e que a válvula opere de maneira eficiente.
Outro erro que pode ocorrer é a falta de documentação adequada durante o processo de calibração. Registrar as leituras iniciais e finais, bem como quaisquer ajustes realizados, é fundamental para futuras referências e para garantir a conformidade com as normas da indústria. Ignorar essa etapa pode dificultar a identificação de problemas futuros e comprometer a eficiência do sistema. Portanto, sempre documente o processo de calibração de forma detalhada, garantindo que todas as informações relevantes sejam registradas.
Além disso, muitos profissionais não realizam testes finais após a calibração. Após ajustar a válvula, é essencial realizar um teste para garantir que a calibração foi bem-sucedida. Ignorar essa etapa pode resultar em problemas não detectados que podem afetar o desempenho do sistema. Para evitar esse erro, sempre faça um teste final após a calibração, observando as leituras do manômetro e garantindo que a válvula opere dentro das especificações desejadas.
Por fim, um erro comum é a falta de manutenção regular das válvulas. A calibração não é um processo único; as válvulas devem ser monitoradas e recalibradas periodicamente para garantir que continuem a operar de maneira eficiente. Ignorar a manutenção pode levar a problemas futuros e comprometer a segurança do sistema. Para evitar esse problema, estabeleça um cronograma de manutenção preventiva que inclua verificações regulares e recalibrações conforme necessário.
Em resumo, a calibração de válvulas é um processo crítico que pode ser comprometido por diversos erros comuns. Preparar adequadamente o ambiente de trabalho, desconectar a fonte de energia, inspecionar a válvula, utilizar instrumentos de medição adequados, seguir as instruções do fabricante, documentar o processo, realizar testes finais e manter as válvulas regularmente são etapas essenciais para garantir uma calibração eficaz. Ao evitar esses erros, os profissionais podem garantir que as válvulas operem de maneira eficiente e segura, contribuindo para o desempenho geral do sistema industrial.
Manutenção e Verificação Pós-Calibração de Válvulas
A manutenção e verificação pós-calibração de válvulas são etapas cruciais para garantir que os sistemas industriais operem de maneira eficiente e segura. Após a calibração, é fundamental implementar um plano de manutenção que assegure o funcionamento contínuo das válvulas, evitando falhas e prolongando a vida útil dos equipamentos. Neste artigo, discutiremos a importância da manutenção e verificação pós-calibração, além de apresentar práticas recomendadas para garantir a eficácia desse processo.
Após a calibração, a primeira etapa na manutenção das válvulas é a realização de uma verificação completa do sistema. Isso envolve inspecionar visualmente as válvulas e os componentes associados, como tubulações e conexões. Durante essa verificação, é importante observar sinais de desgaste, corrosão ou vazamentos. Qualquer anomalia deve ser tratada imediatamente para evitar problemas maiores no futuro. A detecção precoce de falhas pode economizar tempo e recursos, além de garantir a segurança do ambiente de trabalho.
Outro aspecto importante da manutenção pós-calibração é a lubrificação das válvulas. A lubrificação adequada é essencial para garantir que as válvulas operem suavemente e sem resistência. Dependendo do tipo de válvula, a lubrificação deve ser realizada em intervalos regulares, conforme as recomendações do fabricante. A falta de lubrificação pode levar ao desgaste prematuro das peças móveis, resultando em falhas no funcionamento da válvula. Portanto, é fundamental seguir as diretrizes do fabricante e utilizar lubrificantes apropriados para cada tipo de válvula.
Além da lubrificação, a verificação das configurações da válvula é uma parte essencial da manutenção pós-calibração. As válvulas podem sofrer alterações em suas configurações ao longo do tempo devido a fatores como pressão, temperatura e fluxo. Portanto, é importante revisar as configurações periodicamente para garantir que estejam ajustadas de acordo com as especificações desejadas. Isso pode incluir a verificação da pressão de abertura e fechamento, bem como a calibração dos sensores associados. Manter as configurações corretas assegura que a válvula opere de maneira eficiente e dentro dos parâmetros estabelecidos.
Outro ponto a ser considerado na manutenção pós-calibração é a realização de testes de funcionalidade. Após a calibração e a manutenção, é essencial realizar testes para garantir que a válvula esteja funcionando corretamente. Isso pode incluir a abertura e fechamento da válvula em diferentes condições de operação, monitorando as leituras de pressão e fluxo. Os testes devem ser documentados para referência futura e para garantir a conformidade com as normas de segurança e qualidade. Se a válvula não funcionar conforme o esperado, pode ser necessário realizar ajustes adicionais ou até mesmo uma nova calibração.
Além disso, a manutenção preventiva deve ser parte integrante do plano de manutenção pós-calibração. Isso envolve a criação de um cronograma de manutenção regular que inclua inspeções, lubrificação e testes de funcionalidade. A manutenção preventiva ajuda a identificar problemas antes que se tornem críticos, garantindo que as válvulas operem de maneira eficiente e segura. Um cronograma bem definido pode incluir verificações mensais, trimestrais ou semestrais, dependendo do tipo de válvula e das condições de operação.
É importante também considerar a formação e capacitação da equipe responsável pela manutenção das válvulas. Profissionais bem treinados são essenciais para garantir que as práticas de manutenção sejam realizadas corretamente. Investir em treinamento contínuo para a equipe pode resultar em uma operação mais eficiente e segura, além de reduzir o risco de erros durante a manutenção e verificação das válvulas. A equipe deve estar familiarizada com os procedimentos de manutenção, as especificações do fabricante e as melhores práticas do setor.
Outro aspecto relevante é a documentação de todas as atividades de manutenção e verificação. Manter registros detalhados das calibrações, manutenções e testes realizados é fundamental para garantir a rastreabilidade e a conformidade com as normas de segurança. A documentação deve incluir informações sobre as condições de operação, as leituras de pressão e fluxo, os ajustes realizados e quaisquer problemas identificados. Esses registros podem ser úteis para auditorias e para a análise de desempenho ao longo do tempo.
Por fim, a escolha de válvulas de qualidade, como a Valvula esfera tripartida, pode impactar significativamente a eficiência e a durabilidade do sistema. Válvulas de alta qualidade tendem a exigir menos manutenção e oferecem melhor desempenho ao longo do tempo. Portanto, ao selecionar válvulas para o sistema, é importante considerar não apenas o custo, mas também a qualidade e a confiabilidade do equipamento.
Em resumo, a manutenção e verificação pós-calibração de válvulas são etapas essenciais para garantir a eficiência e a segurança dos sistemas industriais. Realizar inspeções regulares, lubrificação adequada, verificação das configurações, testes de funcionalidade e manutenção preventiva são práticas recomendadas que ajudam a prolongar a vida útil das válvulas e a evitar falhas. Investir na capacitação da equipe e na documentação das atividades de manutenção também é fundamental para garantir a conformidade e a eficiência do sistema. Com um plano de manutenção bem estruturado, as indústrias podem operar de maneira mais segura e eficiente, maximizando o desempenho de seus sistemas.
Em conclusão, a calibração de válvulas é uma prática indispensável para assegurar a eficiência e a segurança em sistemas industriais. Através de um processo metódico que inclui a preparação adequada, a realização de ajustes precisos e a manutenção contínua, é possível maximizar o desempenho das válvulas e minimizar riscos operacionais. Além disso, a conscientização sobre os erros comuns e a implementação de um plano de manutenção pós-calibração garantem que as válvulas permaneçam em condições ideais de funcionamento. Investir na calibração e na manutenção das válvulas não apenas melhora a operação dos sistemas, mas também contribui para a segurança dos trabalhadores e a integridade dos processos industriais.